Melt flow rate, originally called melt flow index (MFI), is a measure of the fluidity of melted thermoplastic resin.
It is described as melt mass-flow rate (MFR), expressed in g/10 min, and melt volume-flow rate (MVR), expressed in cm3/10 min.
How Is MFR and MVR Tested?
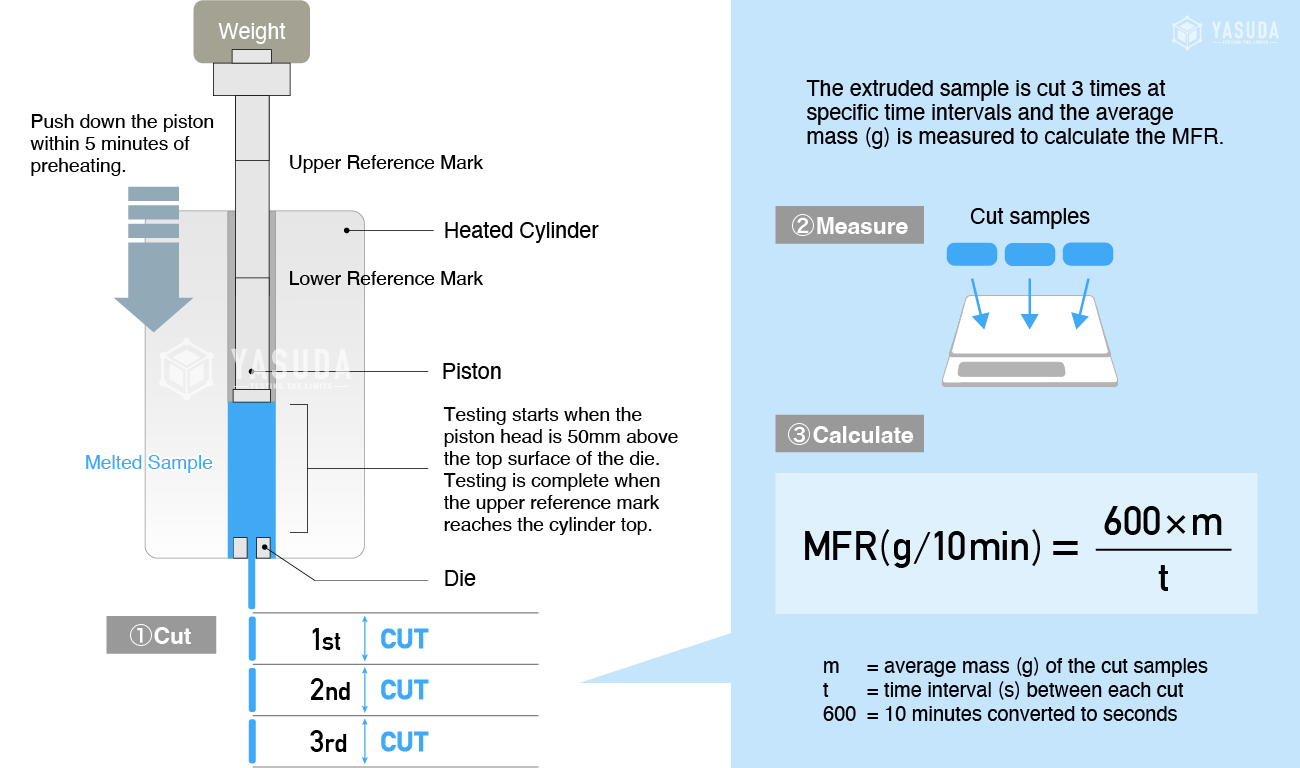
There are several methods used to determine the fluidity of resin, and melt flow test is the easiest method that gives a simple index.
Samples are tested with an extrusion plastometer under conditions and instructions specified in the test standard (e.g., ISO 1133, JIS K7210, ASTM D1238). There are several procedures included in the test standards. The most common are procedures A and B.
In procedure A, in a form of pellets or sometimes powder, the test sample is charged into a heated cylinder. After preheating for a specific period of time, a constant load is applied to the melted sample and extruded from a die at the base of the cylinder. At specific time intervals, the extrudate is cut. The masses of the cut samples are measured to calculate the mass extruded for 10 minutes. (See below for a step-by-step procedure.)
In procedure B, instead of cutting the extrudate at specific time intervals, either of the following is measured:
1) the distance the piston travels for a specified time,
2) the time duration of the piston traveling a specified distance.
Test results are expressed in either MFR (g/10 min) or MVR (cm3/10 min). MFR describes the mass while MVR describes the volume. The MFR can be determined by multiplying the MVR and the density of the melted sample.
MFR corresponds to the molecular weight of resin. MFR is lower for resin with higher molecular weight. Whereas, MFR is higher for resin with lower molecular weight. In most cases, as the MFR value becomes higher, melted resin flows more easily and processing becomes easier. Tensile strength, however, weakens.
Test Procedure
Procedure A
- Fill the heated cylinder with the sample.
- Compress the sample with a packing rod (to remove the gases trapped in the sample).
- Insert the piston into the cylinder and set the test weight.
- Preheat for 5 minutes.
- Start testing when the piston’s lower reference mark reaches the cylinder top (in other words, when the piston head is 50 mm above the top surface of the die).
- At specific time intervals, cut the extruded sample. Cut and take at least 3 strands of extrudate.
- Measure the mass of the strands and calculate the MFR (g/10 min) using the formula as shown in the next section.
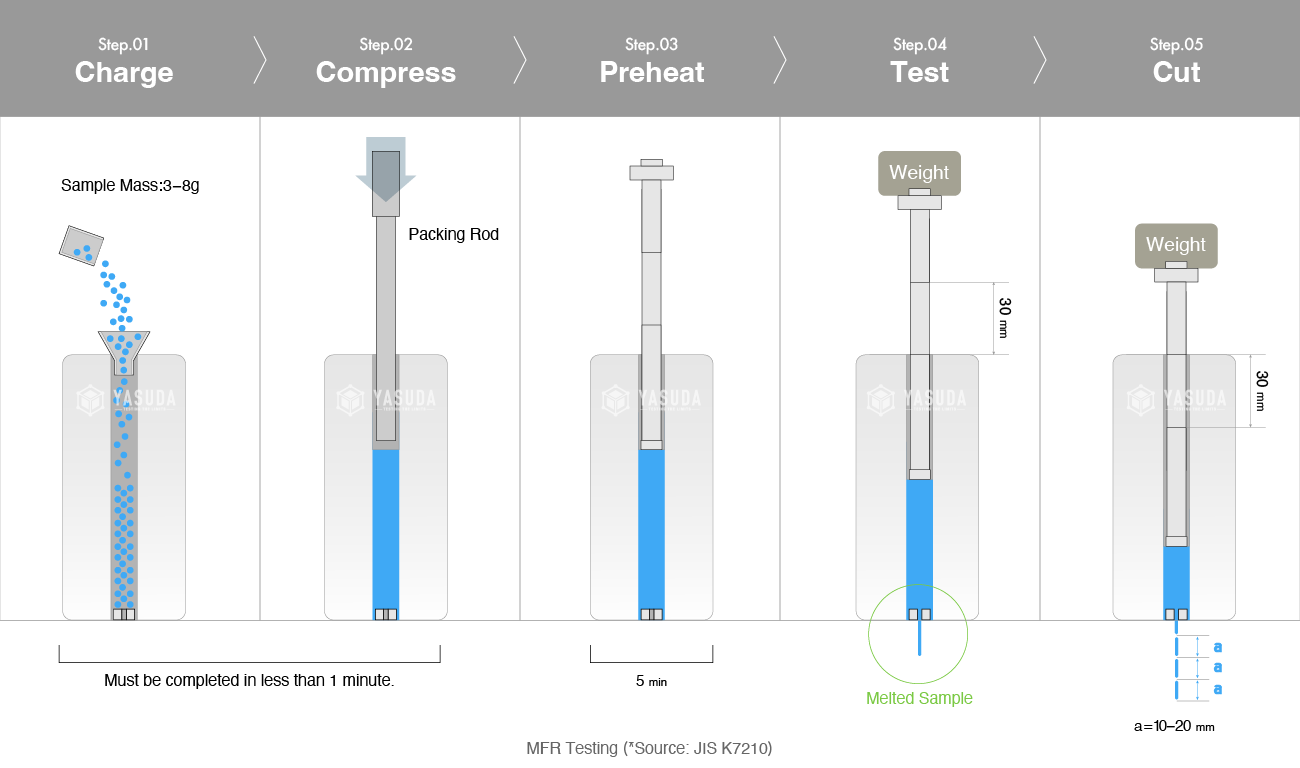
MFR and MVR Calculation
Procedure A
The sample is cut at specific time intervals (e.g., 60 seconds) and the mass of the cut resin is measured.
MFR is given by the following equation.
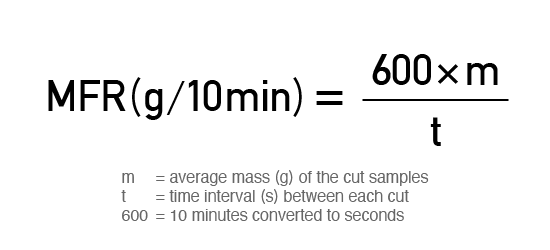
Procedure B
Time how long the piston takes to travel for a specified distance.
MVR is given by the following equation.
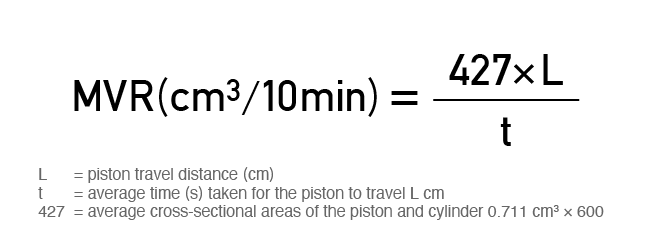
To calculate the MFR from MVR, measure the sample density and use the following equation.
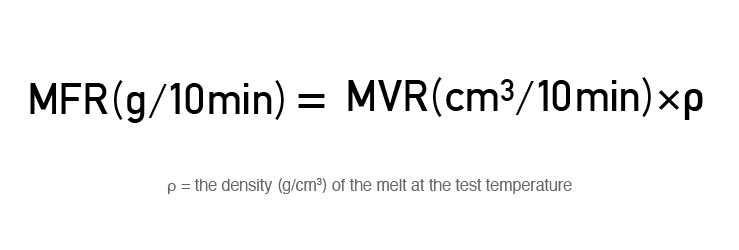
Simple Test, Simple Index
In extrusion molding, as shown in the illustration below, a sample is poured and melted in a heated cylinder, then extruded from a die. Sounds familiar? Melt flow test recreates and also simplifies the process of extrusion molding. Due to its simplicity, MFR is commonly used as a basic index in the quality control of plastic materials.
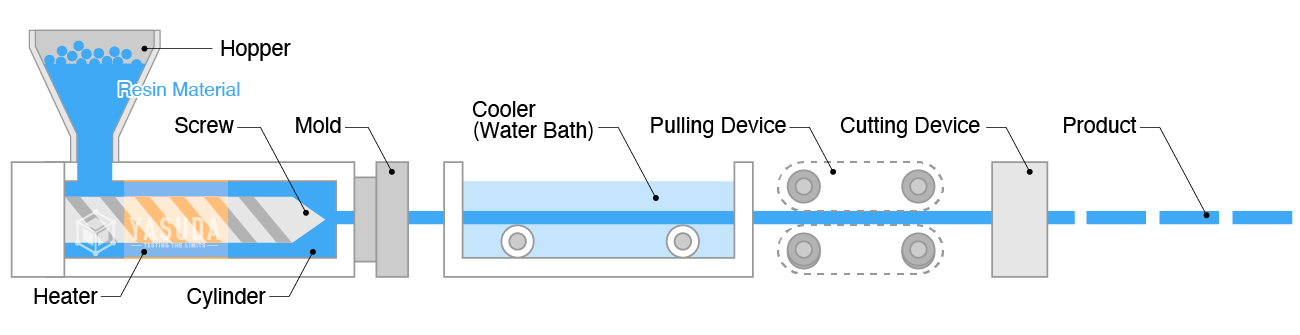
Do Melt Flow Tests Produce Different Results?
MFR and MVR can easily be affected by the moisture (water absorption) of the sample pellet, the resin or filler (such as glass fiber and carbon fiber) content of the sample. The results of melt flow tests can also vary among the different operators due to their difference in their techniques. Therefore, for more consistent results, testing is to be operated by the same person under the same conditions.
As one solution, Yasuda provides automated testers that perform the test for the operator.
Yasuda’s Melt Flow Index Testers
At Yasuda, we have three main models of Melt Flow Index Testers: FWP, SAS, and LABOT. Our No.120-FWP is a manually operated model. Whereas, SAS and LABOT are automatically operated by setting the test conditions in a PC. The latter models also clean the heated cylinder and die during their automatic operation and reduces the work of the operator. Hence, cutting the time for melt flow testing and increasing the efficiency of the operator’s work. By automating the test process, the results are also more stable than when testing is performed by different operators.