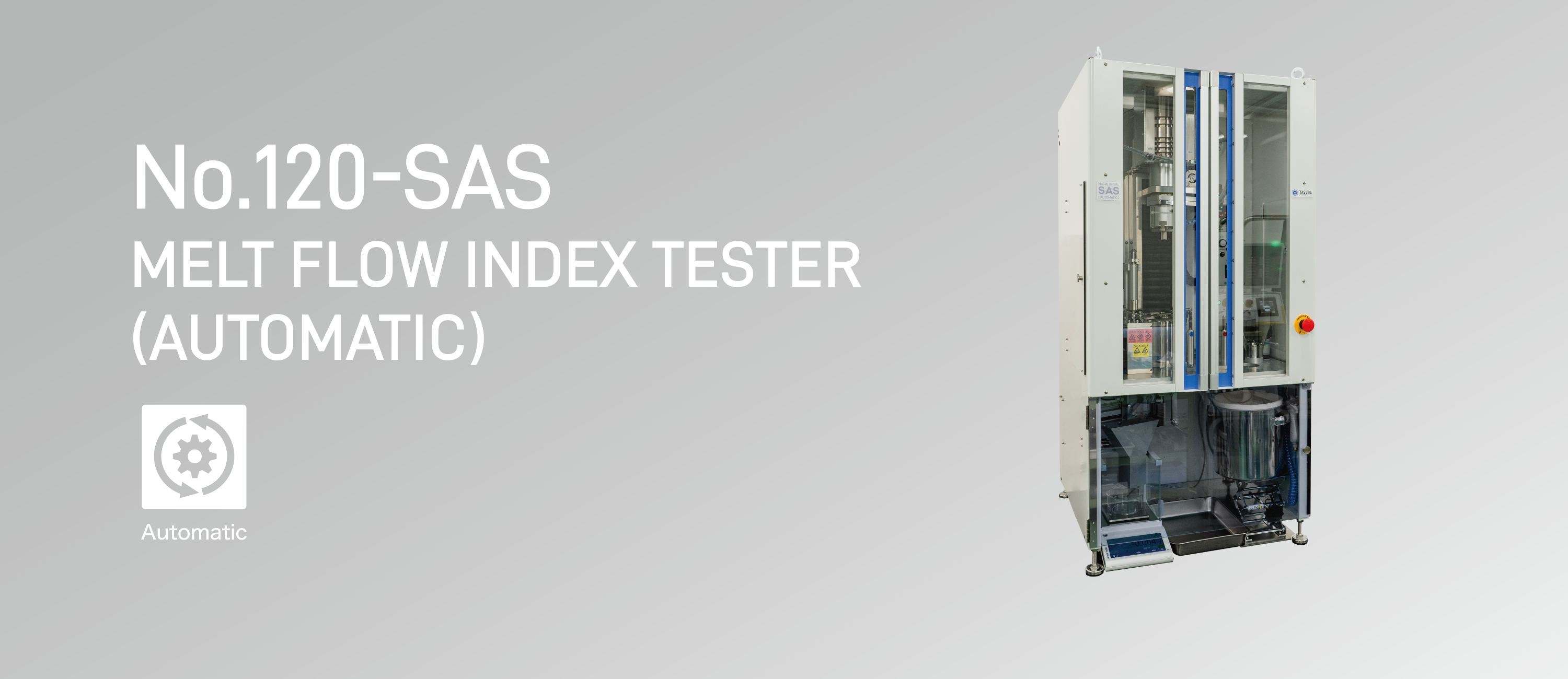
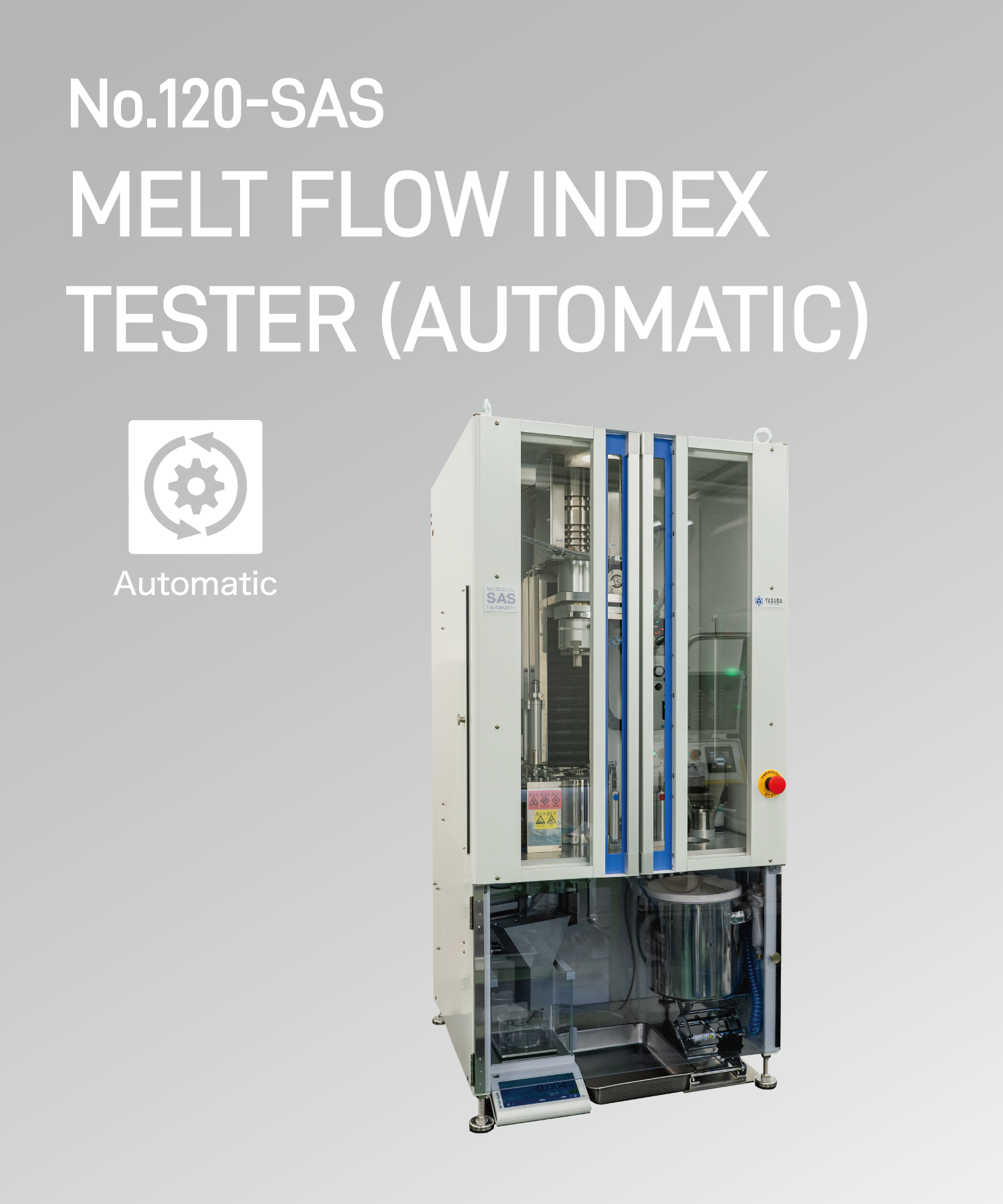
Operation Video
-
Automatic Melt Flow Testing for One Cycle
Reduces human errorSimply set the sample-filled sample cup in the standby area, set up the test conditions, and the melt flow testing will be done automatically. This helps reduce human error related to test procedures and cleaning, improving the reproducibility of test results. We recommend this model for applications where test reproducibility is a must, even if daily test frequency is low. A “3-sample capacity” model that allows three consecutive tests is also available.
-
Simple, Yet Robust
Automatic mechanism with over 20 years of operational durabilityThe full automatic and automatic models utilize a robot arm mechanism, offering an overwhelmingly simple and space-saving design compared to similar products on the market. The mechanism, consisting of a robot arm and arm chuck, performs testing and cleaning with only rotational and vertical movements, minimizing complex actions and reducing error risks. Additionally, the core cylinder of the testing process is fixed in place, enhancing both safety and durability. Due to its simple design, the product is highly durable, and many units continue to operate reliably for over 20 years.
-
Yasuda Seiki’s Unique Sample Cup
Accommodates various sample shapes and material propertiesThe specially developed sample cup used in the automatic and full automatic models allows for direct sample loading into the cylinder. It can handle a variety of sample shapes, including pellets, granules, flakes, sheets, and strips. Additionally, it can accommodate difficult-to-measure powdery samples. The standard sample cup is coated with Teflon on the inner wall, improving its sliding properties for easy loading. For gummy samples, there is an option to replace the inner lining with a Teflon tube.
-
MVR Graphing During Testing
Applicable for validating measurement dataIn melt flow testing, air bubbles mixed into the molten resin during extrusion can cause variability in flow characteristics and affect test results. Yasuda Seiki has developed software that records MVR changes over time along with the test results, using a high-resolution rotary encoder to precisely track piston movement during testing. If air bubbles (entrapped air) are present, this appears as an anomaly in the MVR graph, allowing operators to assess the validity of test results post-test.
-
High-Performance Procedure A Cutter & Automatic Weighing Device
Automates sample cutting and mass measurementThis option automates everything from sample cutting to mass input and MFR calculation of procedure A testing. Yasuda Seiki’s uniquely designed Procedure A Cutter can handle a variety of resin types. After cutting, the sample is cooled by air blow, and the weighing device measures the cut sample’s mass, transfers the measurement value to the software and automatically calculates the MFR value.
-
Powerful Extrusion Mechanism
Extrudes residual material with a 30kW motor outputFor high-viscosity materials with a low flow rate, extruding residual samples after testing can be the most labor-intensive task in MFR testing. The vertical-axis motor, a design shared between the automatic and full automatic models, ensures complete extrusion of residual material, even with low flow rates-viscosity materials. This feature enables safe and effective residual material removal and cylinder cleaning after measurement.
-
Excellent Running Cost Efficiency
Low running-cost operation with only gauze being a primary consumableUnder standard testing conditions, the only consumable needed to run the tester is gauze rolls for cleaning the cylinder and test piston, keeping running costs low.
*In the long term, parts such as the die and piston may require replacement depending on wear.
Reference Standards | JIS K 6719-1/2, K 6921-2, K 6922-2, K 6923-1, K 6924-1, K 6926-2, K 7210-1, ISO 1133-1, ASTM D1238 |
---|---|
Number of Samples | 1 or 3 samples per test cycle (2 kinds) |
Die | φ2.095 ± 0.005 mm, L8.000 ± 0.025 mm |
Piston | Head Diameter φ9.474 ± 0.007 mm, Head Length L6.35 ± 0.10 mm |
Cylinder | Inner φ9.550 ± 0.007 mm, L160 mm |
Temperature Range | Max. 300 ℃ (Option: 400 ℃) |
Initial Weight | 0.325 kgf |
Additional Weight | 1.20 – 21.60 kgf |
Test Method | Method A: Manual (Option: Automatic) Method B: Automatic |
Sample Feeding | Automatic |
Weight Loading | Automatic |
Weight Change | Manual (Option: Automatic) |
Cylinder Cleaning | Automatic (Solvent cleaning can also be automatic) |
Die Cleaning | Automatic |
Piston Cleaning | Manual (Option: Automatic) |
Die Cleaning Rod Cleaning | Manual (Option: Automatic) |
Cleaning Gauze Feeding | Manual |
Data Processing | Method A: Manual (Option: Automatic) Method B: Automatic |
Method B Measuring | Rotary Encoder |
Software | Windows Compatible |
Power Source | AC 200 V, 1-Phase, 15 A, 50/60 Hz |
Air Source | 0.5 MPa or More |
Dimensions / Weight(Approx.) | 1 Hanging: W675× D645 × H1,370 mm/ 200 kg 3 Hangings: W675 × D725 × H1,370 mm/ 220 kg |
In melt flow testing, test loads over 10 kg are required depending on the material, and manually changing the weights can be both burdensome and hazardous. The Automatic Weight Loading Device automates load changes, reducing the physical strain and risk for operators. Additionally, it automatically switches loads based on registered test conditions, allowing continuous testing of samples under different test parameters.
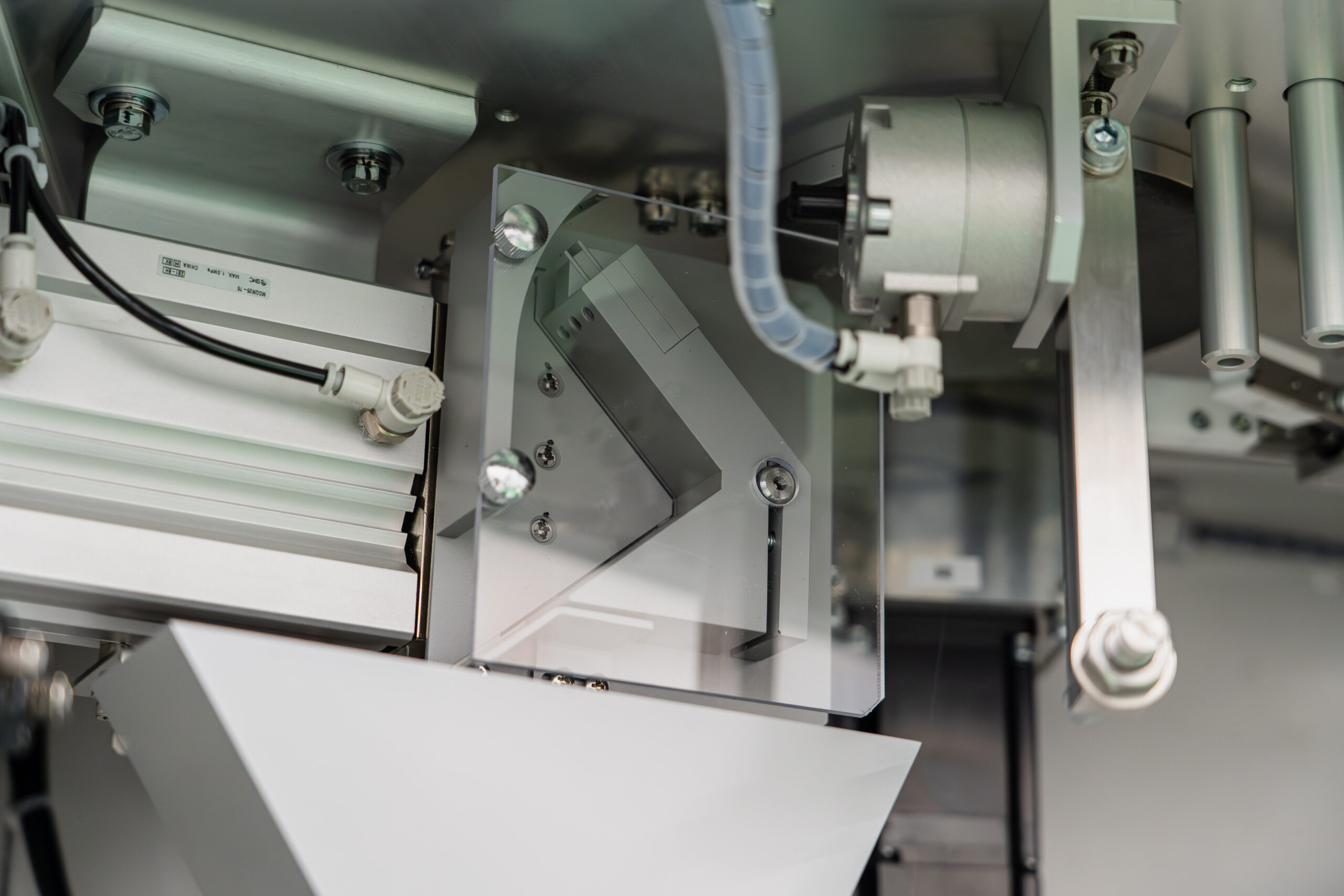
This option automates everything from sample cutting to mass input and MFR calculation of procedure A testing. Yasuda Seiki’s uniquely designed Procedure A Cutter can handle a variety of resin types. After cutting, the sample is cooled by air blow, and the weighing device measures the cut sample’s mass, transfers the measurement value to the software and automatically calculates the MFR value.
While the standard model performs one complete test cycle automatically, this option enables up to three consecutive test cycles. This is recommended for those aiming to further improve efficiency, reduce human error, and utilize the time spent on the testing process.
Contact Us
For over 70 years, Yasuda Seiki’s testing machines have supported quality control and research & development across various industries, meeting the diverse needs of our clients.